Construction professionals that design and manage large projects agree that a concrete product supplier that can quickly create and deliver high volumes of quality products is an absolute must. Yet the rush to finish a high school athletic complex on a tight deadline with atypical foundation specifications revealed that a firm also equipped to provide customized solutions to meet architectural and engineering challenges is priceless.
CHALLENGING PROJECT
The Mercedes High School athletic stadium in Texas required an unusually tall, 71-foot wall. As a result, special load-bearing concrete blocks would be needed for the foundation. Since the approval for project funding came late, architects, engineers and material makers had less than 6 months to complete the project before the first football game in September 2015.
However, construction could not begin until the 12-inch foundation blocks were created with a unique concrete masonry unit (CMU) mix and then tested for a compressive strength of 4,000 psi. Standard concrete block products are 1,900 psi on average, so this project required a customized approach.
Bill Wilson, a 30-year veteran and president of D. Wilson Construction, was selected to build the complex. He knew he would need a major concrete product supplier that could manufacture a large volume of material to meet strict deadlines. The selected firm also needed to have the capability of quickly developing and testing a custom- designed block that could support a tall wall and press box.
SEEKING THE SOLUTION
Innovative Block had set up shop in La Feria, Texas, with a highly automated facility. Company leaders told Wilson that they had never made blocks of the size and compressive strength required for the project, yet they assured him their firm was ideally suited for the challenge. Why? The long-term game plan began with an investment in sophisticated equipment needed to mix and manufacture a variety of concrete products at high volume. They also had recruited an expert staff that embraced creative problem solving.
Yet, construction of the athletic complex could not begin until the specialty blocks had been pushed to extremes to test for compressive strength. Wilson says the key element was the corners of the blocks, because that’s where the weight, or load, of the 71-foot wall would be concentrated.
“That block was the first we had to lay, so we had our concerns. It was a unique stadium project, higher than usual, with a press box on top,” Wilson recalls. Although the mix and compression tests for the blocks ultimately were successful, Wilson knew other challenges, such as quality control, would follow.
PRODUCTION QUALITY
Through the years, Innovative Block perfected methods that guarantee consistent quality and size when manufacturing large volumes. For example, by running German-made machinery, under normal conditions it can produce twelve standard concrete blocks every 20 seconds. But that capacity can be cranked up to 50,000 blocks per day when needed. In the past, some firms could simultaneously produce only two standard blocks with dimensions of 8 x 8 x 16 inches. Also, the new company’s process avoids variances: Block 12 will be exactly the same as Block 1, which makes the mason’s job easier and faster.
Featured Image: The Mercedes stadium project required colored Holland pavers on the walkways that connected the various spaces.
Above: The Mercedes High School athletic stadium in Texas required an unusually tall, 71-foot concrete block wall.
MAKING THE WALL
Miguel Chanin, principle owner of Chanin Engineering, recalls that designing the components of the Mercedes project was challenging because the walls had to withstand the region’s Tier1 rating. The heavy wind loads in the area compare with those in Florida’s Dade County.
“In the end, it looks like a simple building, but it required some extra effort. We knew we’d need a higher strength in the concrete products. When we are looking for a different perspective on block or need a custom solution, Innovative Block provides the necessary expertise. For engineers, that’s invaluable,” he says.
PROJECT COMPLETION
According to both Chanin and Wilson, construction went smoothly and the stadium opened in time for the Mercedes Tigers to fulfill the Texas tradition of Friday Night Lights.
But when fans arrived for the big game, they also got a first look at all the other elements of the project—restrooms, a concessions building, gymnasium, weight room, and an eight-lane track that circles the artificial-turf field. These portions of the complex demanded other realms of expertise that went beyond the speed and efficiency required to create the load-bearing foundation blocks.
For example, the architectural plan for the 6,000-seat Mercedes stadium project required colored Holland pavers on the walkways that connected the various spaces. The pavers are far more aesthetic than concrete walkways, and they also can help reduce run-off and thus pollution, which affects many cities in this nation’s southerly arid regions. Pavers can be permeable and help retain or detain the damaging “first blush” water run-off during torrential rains.
Unique demands accompany nearly every school, corporate or institutional project. Therefore, modern manufacturers of concrete blocks have broadened their services to meet expanding needs and tastes.
COLOR MATCHING, CAST STONE
While concrete blocks are a much needed commodity in the construction industry, these days architects and builders of residential and commercial projects are not satisfied with standard products. Instead, they want customized solutions to upgrade the aesthetics of a design. They know that while gray concrete blocks can be painted, that process creates a maintenance headache that lasts for the life of the building.
To avoid the inconvenience and repeated expense, Innovative Block uses iron oxide Lanxess powdered pigments to maintain color integrity throughout the 60 types of blocks they offer. Custom colors are ideal for campus buildings that wish to display school colors, for example. The process also allows a perfect match of wall and paver colors to better express the vision of the architect and customer.
ONE-STOP SHOPPING
The Mercedes athletic complex and other types of projects suggest that concrete suppliers must offer more than manufacturing capability. By expanding their menu of services, and welcoming creative staff members, modern firms are creating one-stop shopping for construction companies. ■
About the Author: Douglas Glenn Clark is a freelance journalist based in Greater Los Angeles. For more information about Innovative Block products and services, visit www.innovativeblock.com.
_________________________________________________________________________
Modern Contractor Solutions – October 2016
Did you enjoy this article?
Subscribe to the FREE Digital Edition of Modern Contractor Solutions magazine.
Home Project Profiles Demand for Creative Construction Strategies Paves Way for Modern Concrete Block Suppliers
Demand for Creative Construction Strategies Paves Way for Modern Concrete Block Suppliers
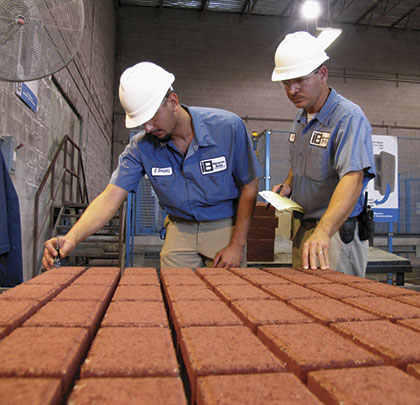