One would expect that an incredibly long highway that connects Mexico and Canada would have tons of songs, myths, and stories written about it. But—not so. The lore of U.S. Route 62 or U.S. Highway 62 (US 62) probably does exist in family stories and communities along the way, but has not yet migrated its way out into popular culture.
Surprisingly, there is no “Get Your Kicks on Route 62” song or a Route 62 television show.
But US 62 is a big deal. It runs 2,248 miles from the Mexico–U.S. border at El Paso, Texas, to Niagara Falls, New York, at the Canada–U.S. border. It is the only east-west United States numbered highway that connects the two countries.
US 62 PROJECT
A 7.5-mi section of US 62 in Oklahoma recently received a rehab. The Oklahoma Department of Transportation (ODOT) project started in Blanchard, Oklahoma, and headed west. Blanchard is part of a rapidly growing area of northern McClain and Grady Counties known as the “Tri-City Area” with Newcastle and Tuttle.
The project section of US 62 is special because the road was built in 2000 when ODOT was switching from conventional HMA to Superpave. The contractor back then was getting used to Superpave and the mix used was too low on oil. Superpave was originated from Strategic Highway Research Program (SHRP), an initiative whose mandate was to improve materials, selection, and mixture design by developing what became known as the Superior Performing Asphalt Pavement System or Superpave.
Unfortunately, the road did not last as well as anticipated—it showed premature wear and deterioration, which necessitated its replacement. In addition, the area where this section of US 62 is located has experienced population growth, so the road is receiving a greater traffic load.
MARKWELL SELECTED
Markwell Paving Co., Oklahoma City, Oklahoma, was selected as the contractor for the U.S. Highway 62 rehab project. Established in 1962, Markwell is a medium-size, third generation, family owned paving company serving the central Oklahoma market with 80 employees. The company offers excavation, soil stabilization, milling, asphalt and concrete paving, sealcoating, and striping.
“A good 97 percent of our work is roadwork,” states Mike Boatman, general superintendent with Markwell Paving. “The US 62 project is exactly the kind of work we do best.”
MILLING THE ROAD
Markwell used its Roadtec RX-700e heavy-duty milling machine for the road work. “The ride quality of the road had deteriorated and required a 2-inch milling depth to establish a base,” Boatman says. “We used a five-worker milling crew to complete the road milling portion of the project.
On its paving team, Markwell Paving had a crew of eight. They placed a 2-inch lift of a locally-sourced RIL (Ridge Intermediate Layer) course directly on top of the uniformly level milled surface. These 14,000 tons of base course contain more oils and additives to bind the milled surface with the top two layers of HMA.
“The RIL mix is very finicky to work with as far as ambient temperature,” states Boatman. “Weather delays we experienced on this project were pretty much during the RIL paving due to temperatures falling outside the material’s application comfort zone.”
THE STEALTH PAVER
The company used its gravity-fed Roadtec SP-100e Stealth paver on the US 62 highway rehab project.
The machine manufacturer describes the paver thusly: “…machine gravity feeds material directly to the auger from the mass flow hopper, replacing the need for slat conveyors, hopper wings, push rollers, and tandem front boggies, thereby significantly reducing maintenance costs and initial purchase price over any conventional 10-foot paver.”
The paver works in tandem with a Roadtec SB-2500e Shuttle Buggy material transfer vehicle (MTV), which provides a steady flow of HMA to the paver. The Shuttle Buggy’s remixing action is designed to reduce thermal and/or material segregation problems. Markwell placed a 2-inch lift of Oklahoma S4 Superpave mix surface course on top of the base course. A quantity of 14,000 tons of Oklahoma S4 Superpave HMA was used. The SP-100e Stealth paver then placed 8,000 tons of Oklahoma S5 Superpave HMA as a mainline finish course on the stretch of U.S. Highway 62.
MEETING THE SPECS
ODOT has studied and tested the thermal cracking resistance of the Oklahoma S4 and Oklahoma S5 HMA mixes and found them to be stiffer, as indicated by higher creep compliance and indirect tensile strength values. Markwell Paving used the HMA mixes specified by ODOT to meet their requirements.
ODOT smoothness requirements are stringent. With a straight-edge test, there can’t be more than a 1/8-inch variance in a 10-foot section.
“We beat the ODOT smoothness test and have paved what I’d argue is likely the smoothest section of US 62 in its entirety,” Boatman states. “We understand that 40 percent of our ability to do so well on a paving job is the equipment, and the Stealth is clearly the significant contributor. And, the other 60 percent is the crew—we have exceptional, experienced people.
SMOOTH FINISHED MAT
As the U.S. Route 62 highway rehab project comes to its end, Mike Boatman reflects on what will be his biggest takeaway from the project … the smoothness of the finished mat.
“Driving the 7.5-mile stretch of Route 62 that we worked on should make any of us with the company feel proud of the work we’ve done. It is definitely the smoothest road in this part of the country.” ■
For More Information: For more information about Markwell Paving and its projects, visit www.markwellpaving.com. For information about Roadtec equipment, visit www.roadtec.com.
_________________________________________________________________________
Modern Contractor Solutions – January 2017
Did you enjoy this article?
Subscribe to the FREE Digital Edition of Modern Contractor Solutions magazine.
The Long, Long Highway
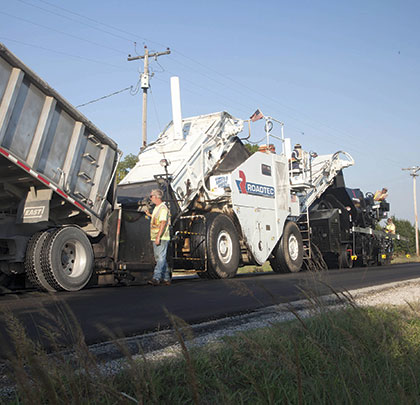