The importance of control in the construction market can’t be overstated. Successful construction contractors have solid control over their costs, means of production, deadlines, and quality of results. Companies are seeking a competitive edge that provides better control over time, improved productivity, and quality that builds loyalty.
Fortunately, Internet-based reporting and documenting systems, such as telematics, enable more effective control over construction assets. Telematics is the integrated use of telecommunications and informatics, and the technology of sending, receiving, and storing information in conjunction with affecting control over remote objects. This remote asset management tool allows contractors to manage all on-site construction assets from one central location.
The benefits of telematics include enhanced real-time communication between equipment and business systems; improved asset management and productivity; improved safety; reduced maintenance and fuel costs; and the possibility of greater theft recovery.
TESTED, PROVEN TECHNOLOGY
A leader in telematics, ZTR Control Systems offers advanced systems that provide a complete end-to-end solution. These systems include hardware, carrier management web and mobile interfaces, pushed data reports, alert callouts, and other features that help simplify telematics program delivery.
“We specialize in capturing data from engine-driven equipment and turning it into useful information to reduce costs and increase revenue,” says general manager Michael Tidy, Connected Asset Division, ZTR Control Systems. “The Machine2Business approach enables real-time, adaptive change in business processes to improve ROI and bottom line business results.”
ZTR Control Systems’ inReach® telematics system provides data and remote diagnostics needed to troubleshoot problems, manage repairs, and prevent further downtime. These systems help contractors know what issues affect a machine located on a jobsite, so they can bring the right tools and parts on service calls to correct the problem.
inReach telematics systems provide real-time information on equipment health, location, utilization, and security. Information is provided through SAE J1939 data and fault codes, Modbus data and alarms, and more. Information is delivered in a usable format through email and/or text message alerts; data can be communicated to a main office, field office, laptop, tablet or smartphone.
“The richness and depth of these online applications are designed to enable smart decisions based on real-time equipment information,” says Tidy. “These applications provide a regional or fleet view of alerts, as well as the ability to drill down to view details on a specific machine.”
USING TELEMATICS IN YOUR BUSINESS
Many contractors gather machine run-time data to calculate current job costs. This information and other historical job cost information can be invaluable for bidding future jobs. Typically the data-gathering process can be expensive, labor intensive, and subject to clerical errors.
ZTR telematics solutions automatically monitor engine hours, and the software can easily be configured to send out alerts when machines are due for maintenance. This feature significantly reduces the chance of machine failure.
Service technicians no longer need to search for the machines they’ve been sent to service—the system’s location capability shows them exactly where the machines are located. These systems also record all completed maintenance tasks, so when equipment is sold, the contractor can create a report showing that all OEM-recommended maintenance was performed on time. This will result in an increase in resale prices that put real dollars back in your pocket.
RETURN ON INVESTMENT
Carefully engineered ZTR telematics solutions provide the right information to the right person at the right time. These systems can increase equipment uptime and efficiency while reducing operating costs. Specifically, ZTR telematics solutions help construction contractors in the following areas:
- Logistics: Improve equipment uptime by providing run hours, location, and information about when and how equipment is used.
- Location: Advanced systems automatically notify you when equipment enters or leaves a site.
- Equipment Availability: Managers can identify idle or underutilized machines that are needed elsewhere.
- Lost Machines: GPS-enabled ZTR telematics systems can locate “misplaced” machines at the touch of a button.
- Curfew: Managers can be alerted when a machine is running outside of normal hours of operation.
- Resale Price Increase: Better records mean better resale value.
- Remote Anti-Start: Machines can be disabled to prevent thieves from driving them off a jobsite at anytime.
- Proactive Maintenance Schedule: Maintenance based on run hours saves time, parts, and expense by avoiding unnecessary maintenance.
- Utilization Tracking: Enables decisions based on documented, actual equipment use.
- Remote Diagnostics: Allows service technicians to bring the right tools and parts on the first trip.
A typical ZTR remote monitoring system includes a telematics control unit (TCU)—the base hardware, a wiring harness, and an antenna. This kit includes everything for basic equipment integration and data communications. Packages also may be customized to include analog and/or discrete sensors, environmental packaging, or other features. ■
For more Information ZTR telematics solutions work with third-party systems and integrate with existing monitoring hardware, or enable bringing information back into a contractor’s business system to complete the end-to-end solution. To learn more about telematics, visit www.ztr.com.
Modern Contractor Solutions, August 2014
Did you enjoy this article?
Subscribe to the FREE Digital Edition of Modern Contractor Solutions Magazine!
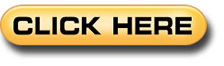